What is Value Stream Mapping (VSM)?
Welcome to our insightful exploration of Value Stream Mapping (VSM), a pivotal tool in the realm of lean management and process optimisation. At its core, VSM is a strategic approach designed to visualise and analyse the flow of materials and information required to deliver a product or service to the customer. This methodical process not only uncovers inefficiencies and identifies waste within a system but also paves the way for transformative improvements.
Through this blog, we will delve into the intricacies of VSM, exploring its key processes, including current and future state mapping, and understanding its profound impact on operational efficiency.
Join us as we unravel the nuances of VSM, a cornerstone in pursuing excellence in process management.
The Meaning of VSM
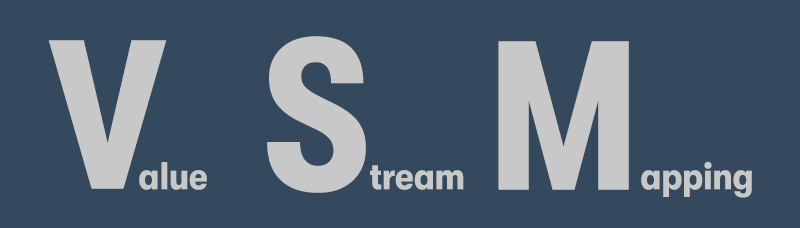
VSM (Value Stream Management) refers to a business methodology and set of practices designed to improve the flow of value to an organisation by identifying, managing, and optimising its value streams. A value stream encompasses all the activities and processes needed to transform a customer request into a good or service. VSM is often associated with lean management and agile methodologies, particularly in software development and IT operations.
What is a Value Stream?
A Value Stream is a fundamental concept in lean management and forms the backbone of Value Stream Management. It refers to all actions, both value-adding and non-value-adding, required to bring a product or service from its initial conception to delivery to the end customer. The idea is to view the flow of value from a holistic perspective, encompassing every step of the process. Here's a detailed breakdown of what constitutes a Value Stream:
Start and End Points
A value stream begins with the initial customer demand or needs and ends with the final product or service delivery to the customer. This encompasses the entire lifecycle of a product or service.
Value-Adding Steps
These steps in the process directly contribute to creating or adding value to the product or service from the customer's perspective. For example, in manufacturing, this could include the actual assembly of a product.
Non-Value-Adding Steps
Often referred to as "waste" in lean terminology, these are steps that do not add any value to the product or service in the eyes of the customer. However, they might be necessary due to current process limitations or organisational structures. Examples include waiting time, transportation, and inventory storage.
Flow of Materials and Information
A value stream includes the flow of materials (in manufacturing) or the flow of work items (in services) and the accompanying flow of information. Understanding how information and materials move through the process is crucial for identifying inefficiencies.
Feedback and Improvement
Value streams also include feedback loops for continuous improvement. Feedback can come from various sources, including customers, employees, and process metrics.
Value Stream Mapping
This is a tool used to visually represent the value stream, identifying all the steps in the process, the flow of materials and information, and areas of waste. It's a key part of lean management practices.
In different contexts, the specifics of a value stream can vary. For instance, a value stream in software development might include stages like requirement gathering, design, coding, testing, deployment, and maintenance. In a manufacturing context, it could involve design, procurement, manufacturing, assembly, and shipping.
The primary goal of analysing and optimising a value stream is to improve the overall efficiency and effectiveness of the process, thereby delivering maximum value to the customer with minimum waste.
What is Value Stream Mapping?
Value Stream Mapping is a lean management tool used to visually document, analyse, and improve the flow of materials and information required to bring a product or service from its conception to the customer. It is a powerful technique for identifying and eliminating waste (non-value-added activities) in a process and implementing more efficient, streamlined operations. Key components and steps involved in Value Stream Mapping include:
Identification of the Value Stream
This involves selecting a specific product or service to map. A value stream map typically focuses on one product or service line to track its flow accurately.
Current State Mapping
The first map created is the "current state" map. This visualises how things currently operate. It includes all the steps, delays, and flows of material and information presently involved in delivering the product or service. It's essential to gather detailed and accurate data for this phase, including cycle times, wait times, inventory levels, etc.
Identify Waste
Using the current state map, you can identify areas of waste. In lean terminology, waste can be overproduction, waiting, transporting, overprocessing, excess inventory, unnecessary movements, and defects.
Future State Mapping
After analysing the current state and identifying waste, the next step is to create a "future state" map. This map represents an improved version of the current state, showing how things should operate with the identified waste removed or minimised. The future state map sets the goals for a leaner operation.
Implementation Plan
This involves creating a plan to transition from the current state to the future state. It includes specific actions, assigning responsibilities, setting timelines, and determining necessary resources.
Continuous Improvement
Value Stream Mapping is not a one-time activity. After implementing the future state, monitoring, reviewing, and continuously improving is essential. New inefficiencies or areas for improvement might emerge, requiring additional VSM cycles.
Value Stream Mapping is widely used in manufacturing. Still, its principles are equally applicable in service industries, healthcare, software development, and virtually any environment where a product or service is being delivered.
What Are the 3 Main Types of Value Stream Mapping?
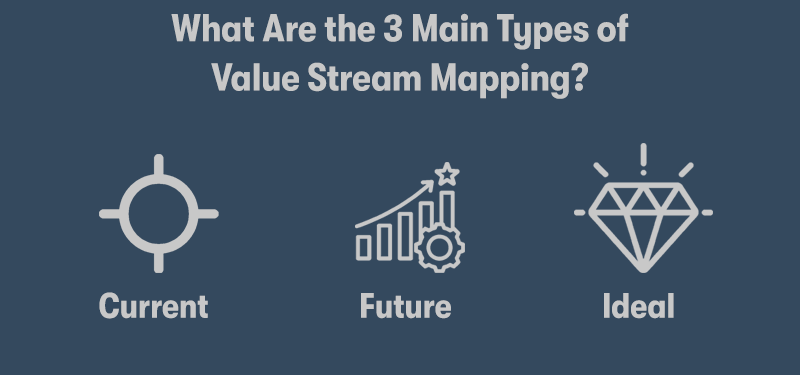
Value Stream Mapping is a versatile tool used in lean management to analyse and design the flow of materials and information required to bring a product or service to a customer. While VSM is a singular concept, it can be categorised into three main types based on the focus and scope of the mapping. These types are:
- Current State Value Stream Mapping
- Future State Value Stream Mapping
- Ideal State Value Stream Mapping
Current State Value Stream Mapping
Focus: This type of VSM is centred on documenting the existing condition of the processes.
Purpose: The goal is to gain a clear and comprehensive understanding of the current process flow, including all steps, delays, and flows of material and information.
Application: It's used to identify inefficiencies, waste, and bottlenecks in the current process. This map serves as the baseline for improvement.
Future State Value Stream Mapping
Focus: This VSM type is about envisioning an improved version of the current state.
Purpose: The aim is to design a more efficient and effective process flow that addresses the issues identified in the current state map.
Application: It involves setting goals for improvement, such as reduced waste, shorter cycle times, and improved quality. The future state map provides a roadmap for implementing changes.
Ideal State Value Stream Mapping
Focus: Ideal state VSM represents the ultimate, optimised process that could be achieved if all constraints were removed.
Purpose: The purpose is to imagine the best possible scenario where the process is completely optimised and all forms of waste are eliminated.
Application: While often theoretical, this mapping type encourages long-term visionary thinking and sets a direction for continuous improvement beyond immediate practical limitations.
Often, organisations start with the current state mapping, use insights gained to create the future state map, and then consider the ideal state as a long-term goal.
Value Stream Mapping is not a one-time activity but a continuous process. As improvements are made, new current state maps are drawn, leading to a cycle of ongoing improvement.
Maps can be customised depending on an organisation's specific needs and goals. The core principles, however, remain focused on identifying value, eliminating waste, and improving the flow of value to the customer.
Each type of VSM has its specific role and benefits in the continuous improvement journey of an organisation. They collectively help in visualising how things are and how they could be better, guiding strategic decisions and operational improvements.
Value Stream Mapping Process
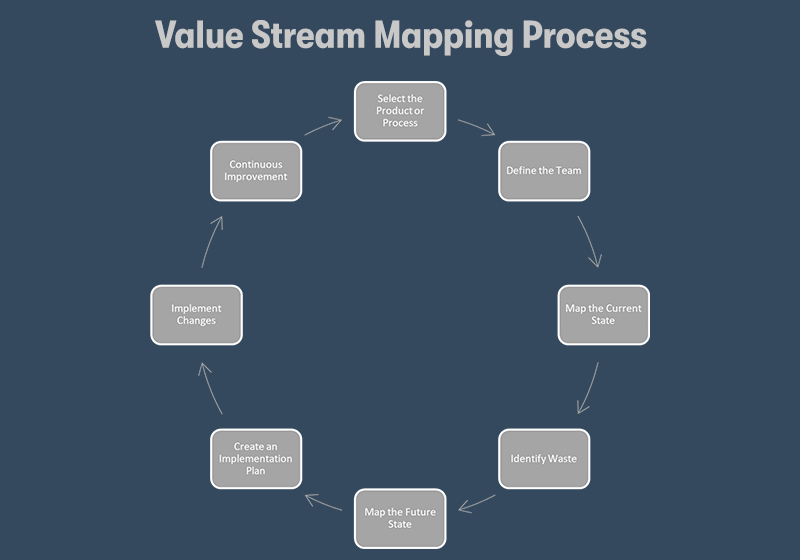
- Select the Product or Process
- Define the Team
- Map the Current State
- Identify Waste
- Map the Future State
- Create an Implementation Plan
- Implement Changes
- Continuous Improvement
How to Create a Value Stream Map?
The Value Stream Mapping (VSM) process is a systematic approach used to analyse and improve the flow of materials and information required to deliver a product or service to a customer. It's a key tool in Lean methodologies aimed at identifying waste and inefficiencies in a process. The VSM process typically involves the following steps:
Step 1: Select the Product or Process
Identify the Product/Service: Choose a specific product or service for which the value stream will be mapped. This selection should be aligned with your business goals and improvement priorities.
Step 2: Define the Team
Assemble a Cross-Functional Team: Bring together individuals from various departments involved in the process. This ensures a comprehensive view and understanding of the process from different perspectives.
Step 3: Map the Current State
Gather Data: Collect data on the current process, including cycle times, wait times, inventory levels, and work in progress.
Document the Steps: Visually map out each step of the process from start to end. This includes both value-adding and non-value-adding steps.
Identify the Flow: Show the flow of materials and information throughout the process.
Use Symbols: Standard symbols are used to represent different stages, actions, and flows.
Step 4: Identify Waste
Analyse the Map: Look for signs of waste, such as delays, bottlenecks, unnecessary movements, overproduction, and excess inventory.
Categorise Waste: Use Lean principles to categorise waste into transportation, inventory, motion, waiting, over-processing, overproduction, and defects.
Step 5: Map the Future State
Envision Improved Processes: Based on the current state analysis, design a future state map that eliminates or reduces the identified waste.
Set Improvement Targets: Determine goals and benchmarks for the improved process.
Step 6: Create an Implementation Plan
Develop Actionable Steps: Outline the specific steps needed to achieve the future state, including resource allocation, timelines, and responsibilities.
Prioritise Actions: Some changes might be implemented quickly, while others may require more time and planning.
Step 7: Implement Changes
Execute the Plan: Begin implementing the improvements. This often involves changing processes, retraining staff, and investing in new tools or technologies.
Monitor and Adjust: Regularly review the progress and make adjustments as necessary.
Step 8: Continuous Improvement
Iterative Process: VSM is not a one-time activity. Regularly update the value stream map to reflect changes and look for new opportunities for improvement.
Engage the Team: Continuously involve the team in identifying and implementing improvements.
Key Points to Remember:
- Customer Focus: Always keep the end customer's needs in focus. The primary goal is to deliver more value to the customer efficiently.
- Data-Driven: Decisions should be based on accurate and relevant data.
- Collaboration: Success in VSM relies on collaboration across different departments and levels within the organisation.
- Flexibility: Be prepared to adapt the plan as new information or challenges arise.
Value Stream Mapping is a powerful tool for visualising work processes and identifying areas for significant improvement. It's particularly effective in environments reducing waste and improving flow can substantially improve efficiency, quality, and customer satisfaction.
What are the Benefits of Value Stream Mapping?
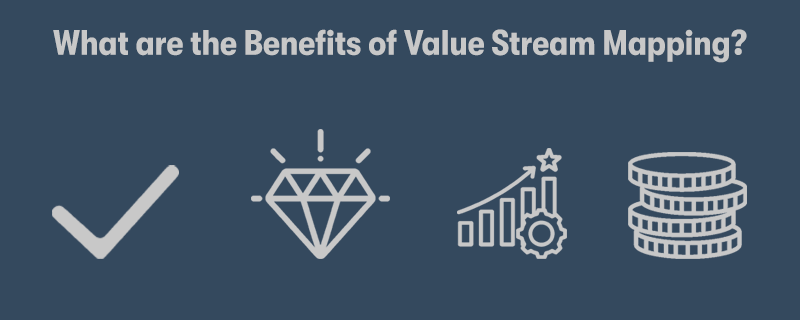
Value Stream Mapping is a powerful tool in lean management and continuous improvement practices. It offers several significant benefits to organisations that implement it effectively. These benefits include:
Enhanced Process Understanding
Visualises the Entire Process: VSM provides a clear visual representation of the flow of materials and information through the entire process, making complex processes easier to understand.
Identifies Interdependencies: Helps in understanding how various parts of the process are interconnected, promoting a holistic view of operations.
Improved Efficiency and Productivity
Identifies Waste: VSM helps identify non-value-adding activities (waste) in the process, such as delays, bottlenecks, unnecessary movements, or overproduction.
Streamlines Workflows: By eliminating or reducing waste, processes can be streamlined, leading to more efficient and productive operations.
Better Quality and Customer Satisfaction
Focus on Customer Value: The mapping process is driven by what adds value from the customer's perspective, leading to improved quality and customer satisfaction.
Reduces Defects and Errors: The likelihood of errors and defects can be reduced by streamlining the process and removing unnecessary steps.
Enhanced Collaboration and Communication
Cross-Functional Collaboration: VSM involves team members from various departments, enhancing cross-functional understanding and collaboration.
Common Understanding: The visual nature of a value stream map creates a shared understanding of the process and challenges among team members.
Data-Driven Decision Making
Quantifiable Metrics: VSM uses data collected during the mapping process, such as cycle times and wait times, enabling data-driven decision-making.
Sets Clear Improvement Targets: The process helps set specific, measurable goals for process improvement.
Support for Strategic Planning
Aligns Operations with Business Goals: By improving efficiency and customer satisfaction, VSM helps align operational processes with broader business objectives.
Facilitates Long-Term Planning: The future state map provides a roadmap for long-term operational improvements and strategic planning.
Flexibility and Adaptability
Identifies Flexibility in the Process: Helps in understanding how changes in demand or conditions can affect the process, supporting more adaptable and flexible operations.
Continuous Improvement: Encourages a culture of continuous improvement, where processes are regularly evaluated and updated.
Cost Reduction
Reduces Operational Costs: By eliminating waste and improving process efficiency, VSM can significantly save costs.
Optimises Resource Utilisation: Ensures resources are used more effectively, reducing excess inventory and improving resource allocation.
Enhanced Competitive Advantage
Faster Time-to-Market: Streamlined processes often result in shorter lead times, enabling more immediate delivery of products or services.
Strengthens Market Position: Improved efficiency, quality, and customer satisfaction can enhance a company's competitive position in the market.
In summary, Value Stream Mapping is not just a tool for identifying and cutting out waste; it's a comprehensive approach to process improvement that can have a far-reaching impact on an organisation's efficiency, productivity, and customer satisfaction. By providing a clear roadmap for improvement, VSM helps organisations in adapting to changing market demands and staying competitive.
Final Notes on What is Value Stream Mapping?
In conclusion, our exploration of Value Stream Management and its associated concepts has been illuminating. We've delved into the essence of a Value Stream, the intricacies of Value Stream Mapping, and the steps to create a VSM template. Our journey covered the three main types of VSM and the four critical steps involved in the mapping process, concluding with the diverse benefits VSM offers. This comprehensive discussion underscores VSM's significance in enhancing process efficiency, fostering collaboration, and driving continuous improvement in various industries.
As we wrap up, remember that the journey to operational excellence is ongoing, and tools like VSM are pivotal in navigating this path successfully. May your endeavours in streamlining processes and maximising value be fruitful and enlightening.